Overview
In our recent project collaboration with St Margaret’s School, Furphy Foundry showcased its prowess in translating vision into reality. The client’s layout design served as our guide, leading us to manufacture to their precise measurements. Our in-house design team seamlessly transformed these measurements into detailed site and shop drawings, ensuring every element interacted harmoniously with the surrounding landscape features which consisted of shelters and garden beds. The critical success factor lay in the precision of the measurements, a feat we achieved through thorough attention to detail during manufacturing.
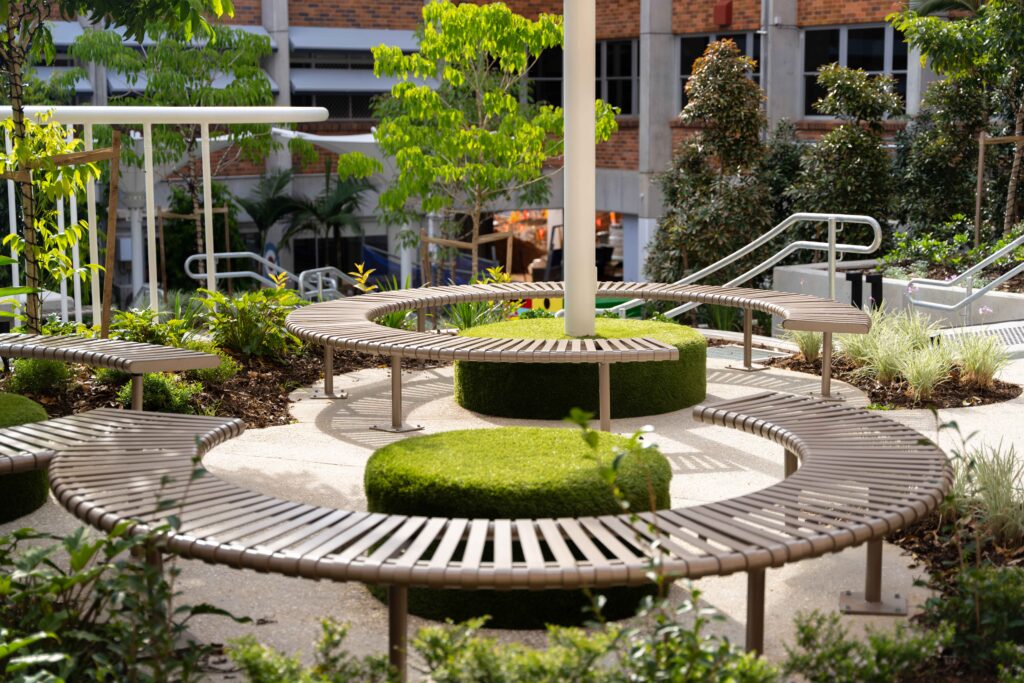
Championing innovation, Furphy leveraged its expertise to navigate challenges and deliver excellence. Despite facing constraints due to the location’s limitations on heavy machinery, our team devised a solution by designing sections small enough for manual installation. Utilizing environmentally friendly E-Coat on Mild Steel, followed by a powder coat top coat, not only fortified the structure against corrosion but also expedited the manufacturing process, while maintaining an impeccable finish. Furphy provided a comprehensive installation plan and instructions, ensuring a seamless transition from fabrication to installation. Each section, labeled with a weld stamp corresponding to the layout plan, guaranteed clarity and precision on-site, with a total of 135 meters crafted into 114 individual sections. This project exemplifies Furphy’s commitment to excellence and innovation, transforming client visions into reality.
Materials & Finishes
To enhance durability and environmental friendliness, Furphy Foundry opted for E-Coat mild steel components. This anti-corrosion treatment not only provided superior protection but also sped up the process compared to traditional galvanizing methods. The final powder coat finish added visual appeal, ensuring that the furniture would withstand heavy usage and still maintain its aesthetic appeal over time.
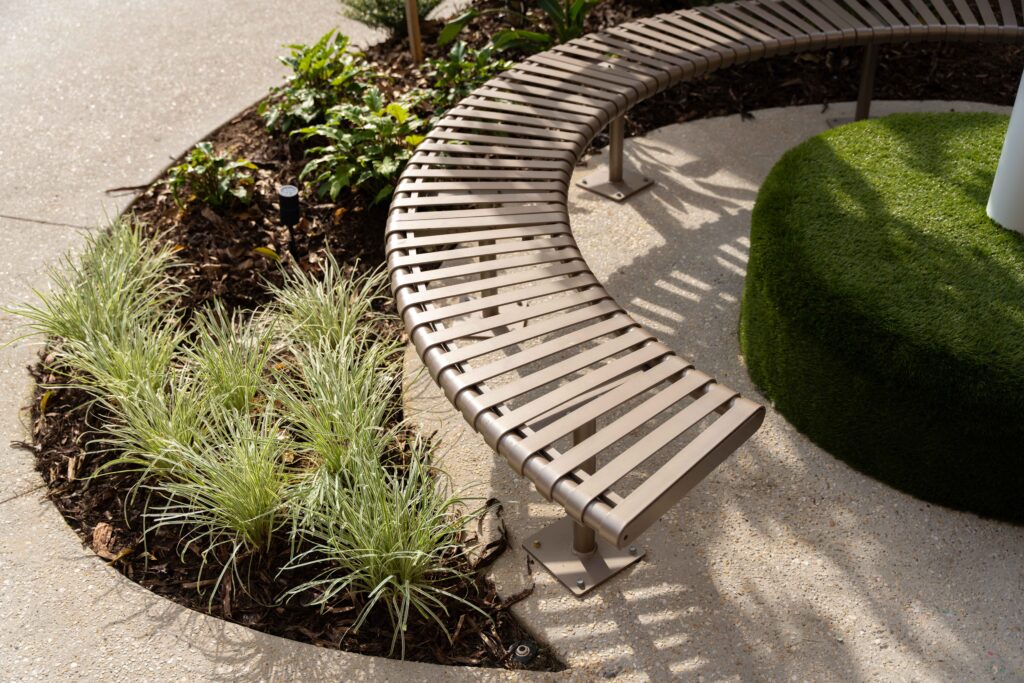
Challenges
One of the key challenges was the site’s limited access for heavy machinery which made it difficult for transporting and installing large sections. Furphy Foundry’s solution was to design smaller, manageable sections that could be easily handled by the installation team. This thoughtful approach was critical to the project’s success, demonstrating Furphy’s ability to navigate logistical constraints effectively.
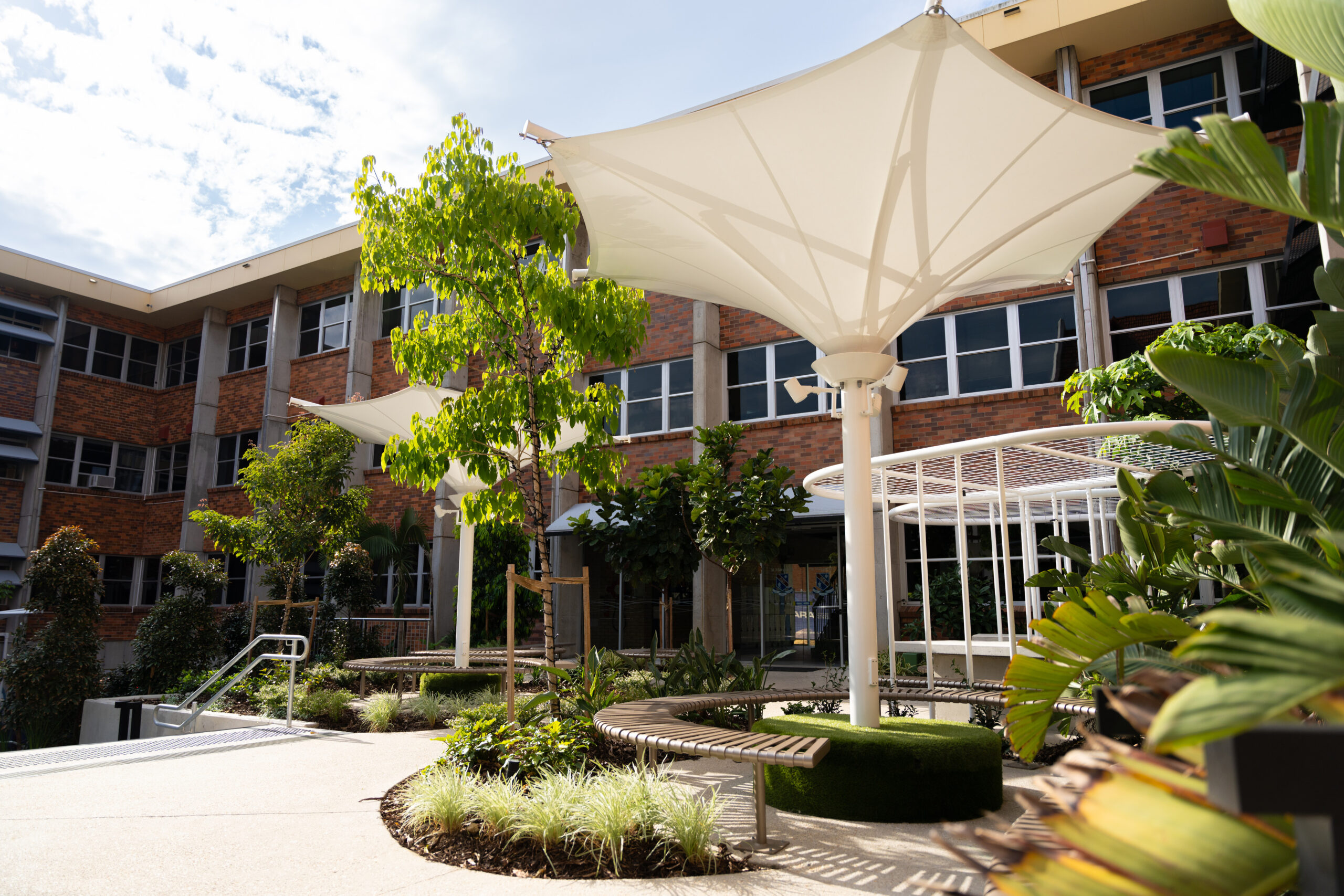
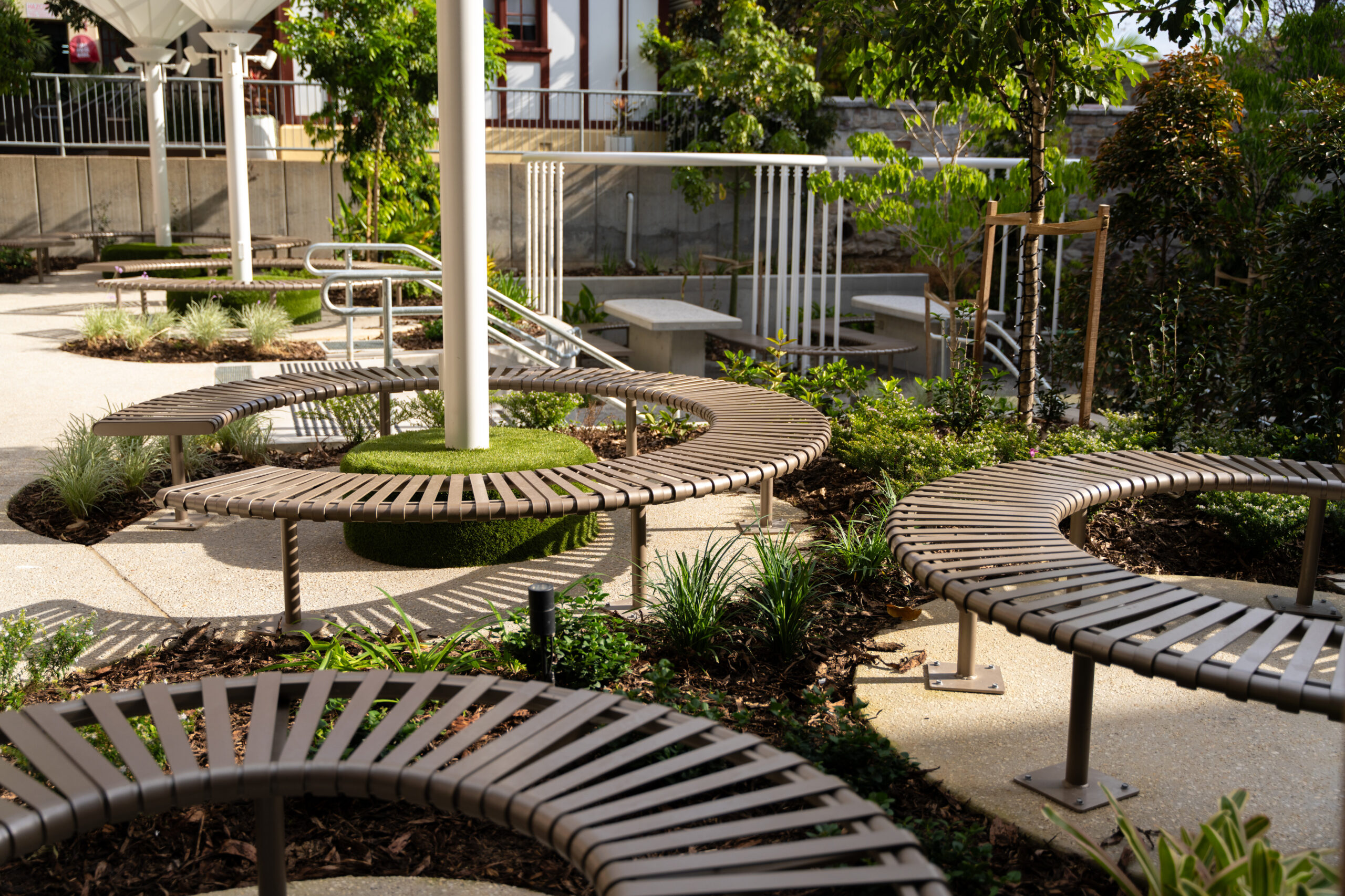
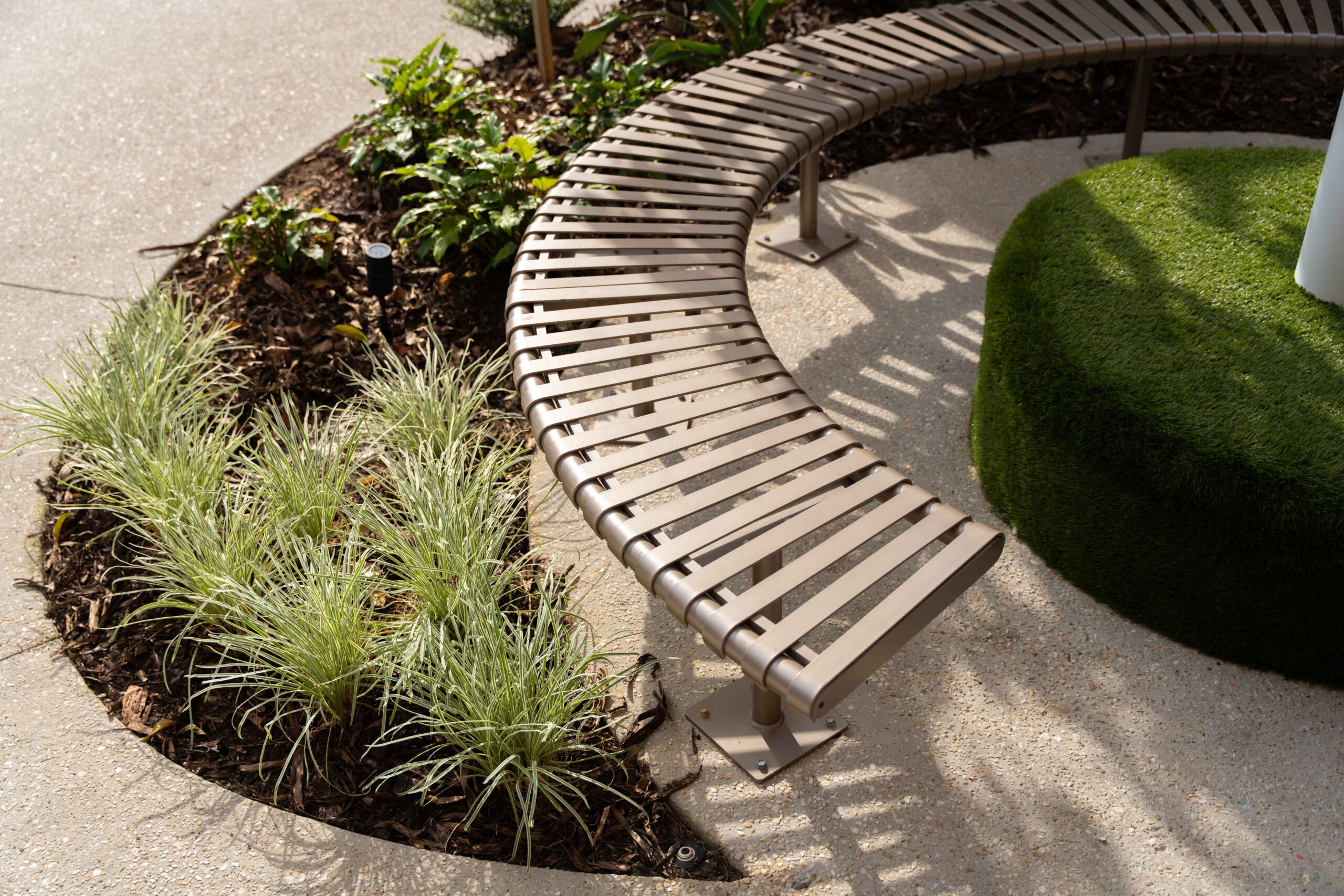
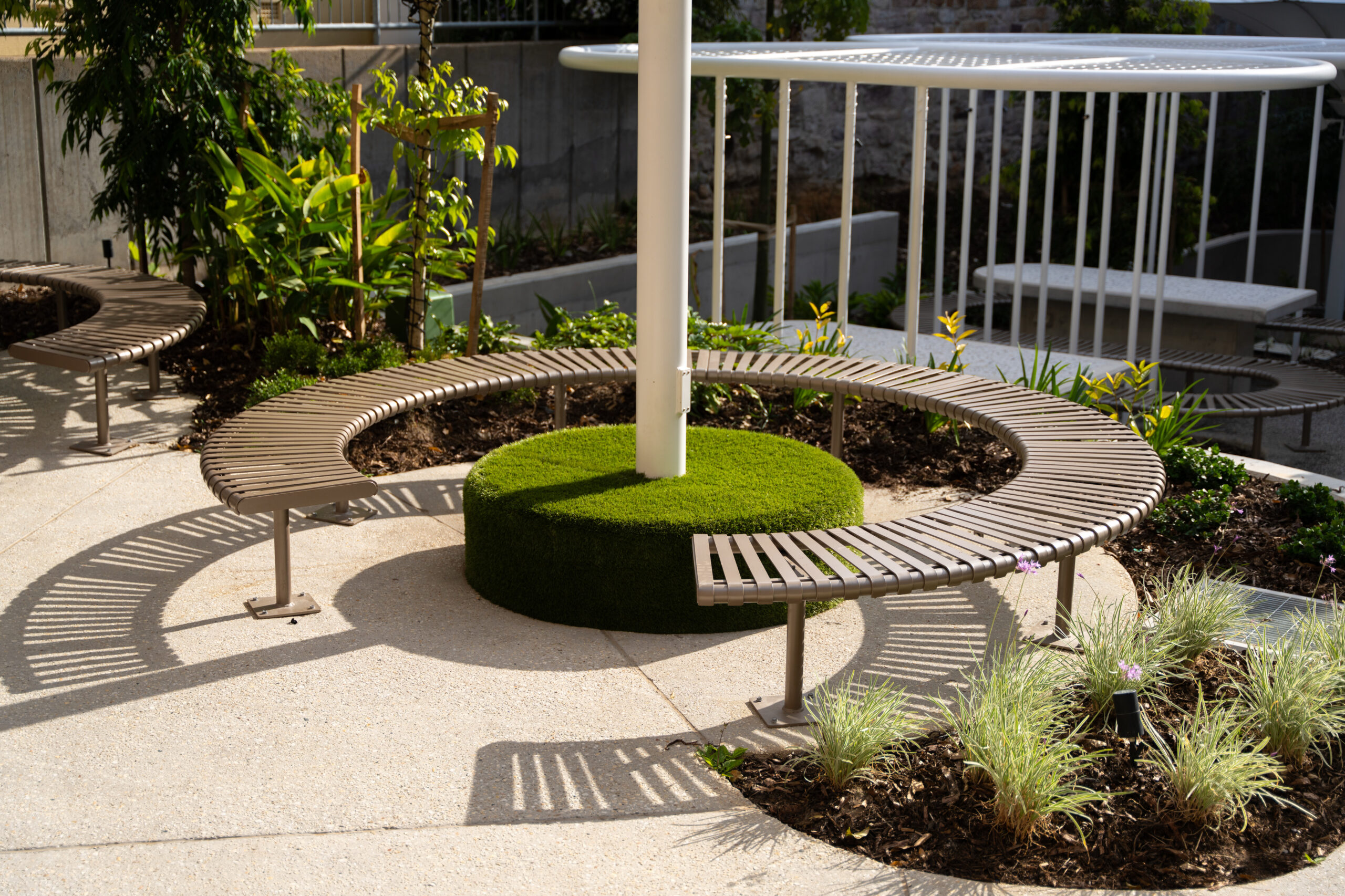
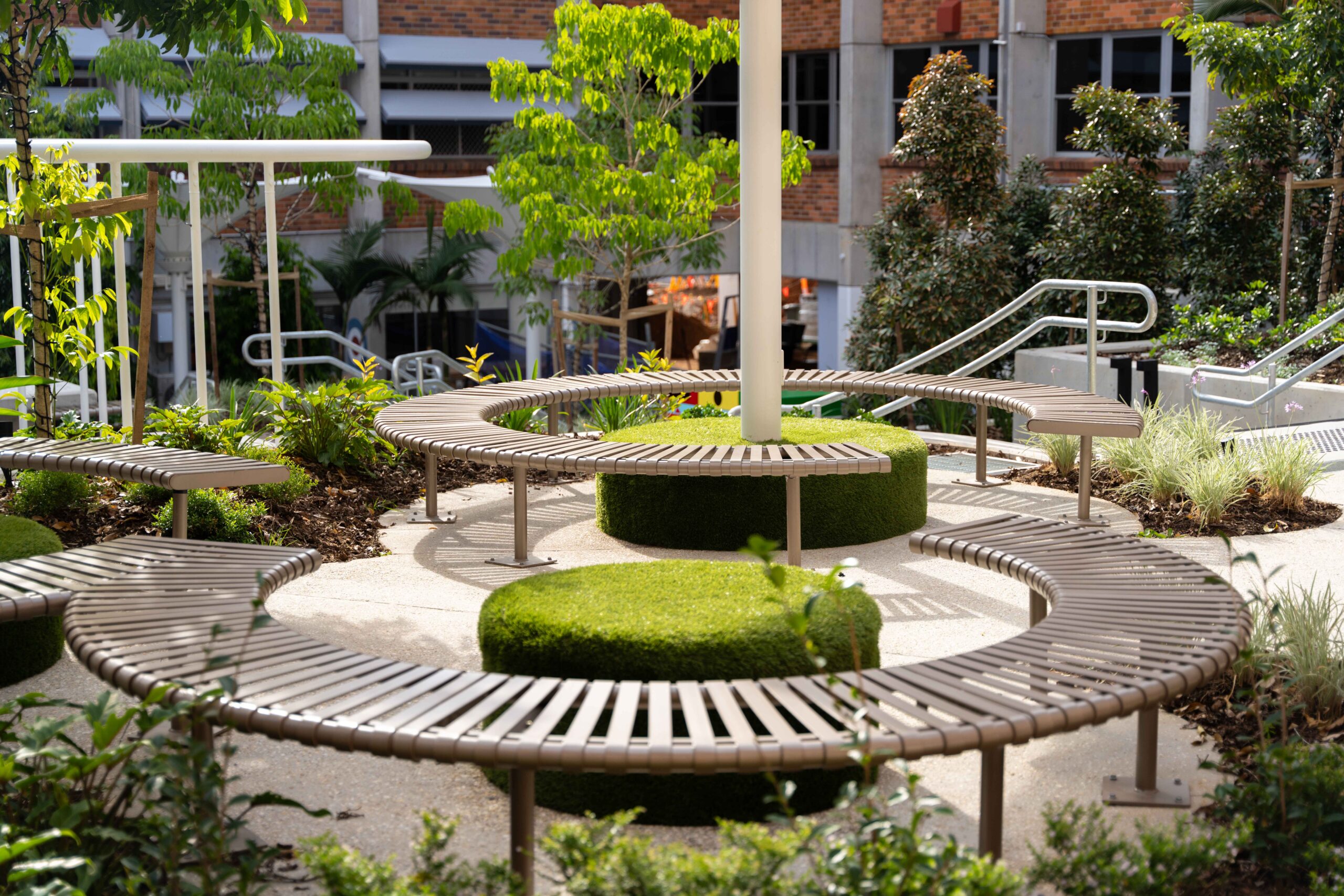